CAST IRON MANUFACTURING
Mastering a Challenging Material. Thanks to their high level of machinability, cast iron alloys have entered the modern era of manufacturing in industries from automotive to heavy machinery. Despite these advantages, cast iron’s complex nature offsets some of its machining ease. Its abrasiveness shortens tool life and produces uneven wear, and its porous structure creates micro-interruptions that complicate the process of producing perfectly straight holes.
To achieve this type of toolholding success, look to the REGO-FIX powRgrip® system for extremely low runout and vibration – performance that increases tool life by as much as 400-500%, with even wear across the cutting edge that eases regrinding and sharpening operations. Our press-fit powRgrip holders provide the process security and performance that hydraulic or shrink-fit holders can’t match, even in deep-hole drilling and gundrilling applications. Available in a wide selection of holder types, lengths and diameters, all balanced for steep taper and HSK toolholders, our powRgrip collets come in inch and metric sizes up to an H9 shank.
REGO-FIX supplies the industry’s widest variety of collet and toolholder types, lengths and diameters, all with unfailing repeatability, vibration damping and lasting quality. That lineup includes small-diameter and high-speed holders and systems for cutting tools down to 0.0079″ (0.2 mm) in diameter. Our full selection of clamping and torquing devices, along with a wide variety of other accessories, assures you of the flexibility you need to meet any customer requirement.
powRgrip Means Results
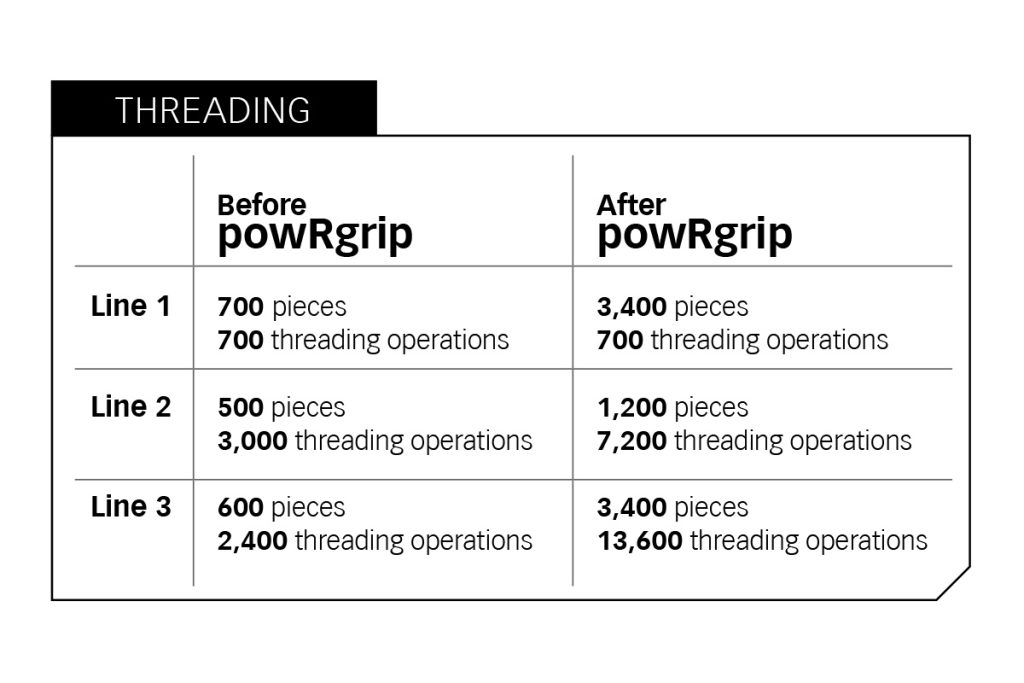
powRgrip improves threading productivity
An experienced automotive and heavy-equipment producer implemented a customized powRgrip system to handle cast iron machining challenges for threading applications. On three threading production lines, powRgrip increased output by 2.4x to 5.6x per line, saving the manufacturer about $225 per day.
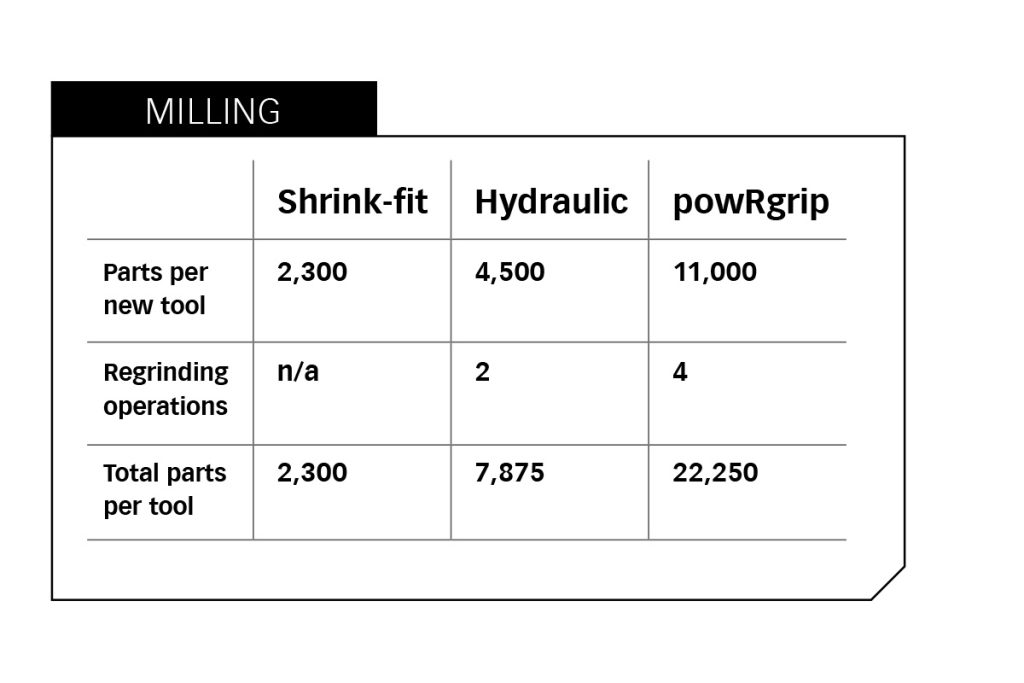
powRgrip improves tool performance and regrinding
A Tier 1/Tier 2 automotive manufacturer of cast iron crankshaft components struggled to maintain tool life on 25 mm six-flute cutters. Shrink-fit holders made tool wear uneven and regrinding unprofitable. Hydraulic holders compromised tool performance at the edge of the workpiece. With powRgrip, total parts per tool increased nearly 10x over shrinkfit holders and more than 2.75x over hydraulic holders.
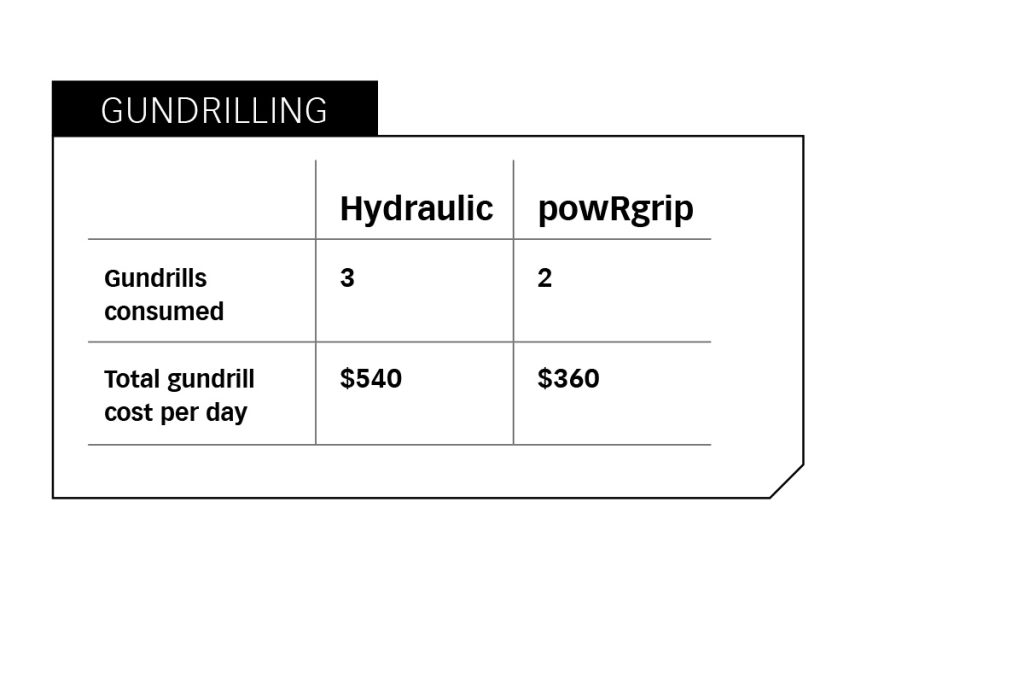
powRgrip simplifies automotive drilling
An automotive supplier needed complete rigidity for a difficult gundrilling application during engine production. With powRgrip instead of hydraulic toolholding, daily tool use dropped from three gundrills to two, reducing tool cost by 33%.
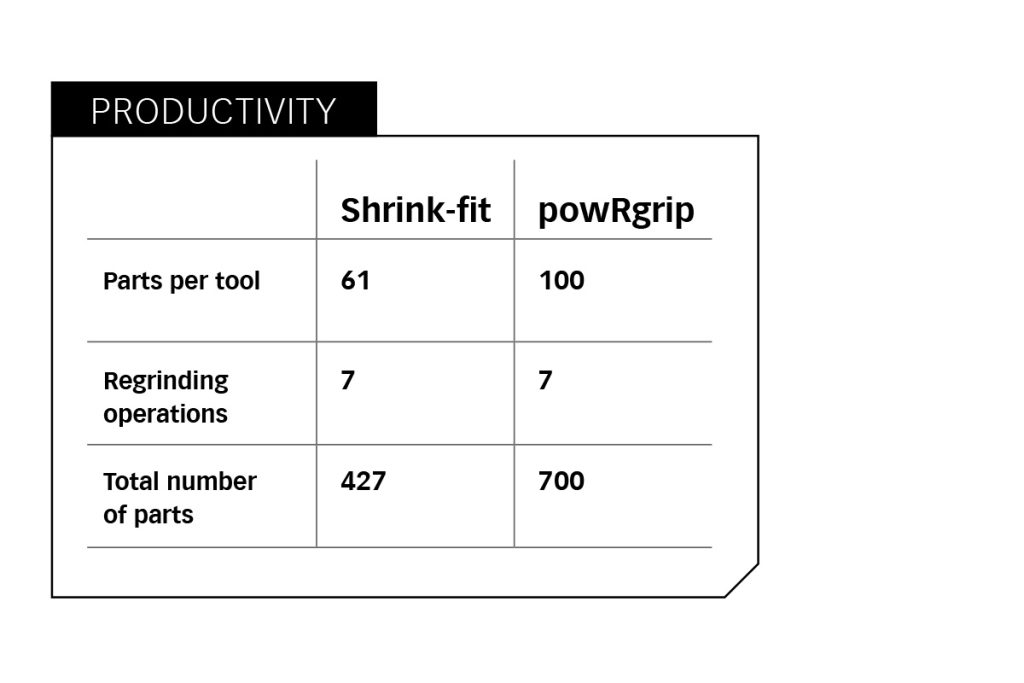
powRgrip supercharges cylinder head production
A leading heavy equipment manufacturer struggled to overcome the impact of shrink-fit toolholders on tool life. With powRgrip, productivity per tool increased by 40%.